Optimising partnership and costs
At Delfield Precision Engineering we help you solve and fulfil your complex precision assembly needs by combining under one roof our capabilities in lead lining, aluminium dip brazing, CNC machining, assembly and painting.
We supply a wide range of industries including Aerospace, Defence, Electronics, Railway and Water Treatment. However, our specialisation is in the Healthcare and Medical Systems industry. We are a global leader in the manufacturing of X-ray tube housings for medical imaging systems. We supply the leaders of the medical imaging industry (Computed Tomography, Vascular imaging, Nuclear Medicine) across their worldwide operations.​
​
We approach every project not as providing a part, but as designing and manufacturing components that will play a critical role in finished products. We are recognised for delivering reliable quality and controlling all critical quality and safety requirements, tolerances and attributes. We gain our customers’ confidence and trust by collaborating with you to find the optimal solutions, being a reliable, efficient partner helping you maximise your return on investment.
To optimise your costs, we offer a unique, engineering-driven process designed to identify potential efficiencies in design, materials and finishing. Then our team of highly skilled and experienced machinists translates each design into flawless components.
​
We continually invest in expanding and modernising our facilities and equipment to support every phase of the process, from prototyping, finding solutions for our customers and on-time delivery. In particular, we command specific know-how on the design and production of leak-tight aluminium vessels with complex geometries thanks to our combination of dip brazing and leak testing capabilities. We are one of the very few providers of aluminium dip brazing services throughout Europe. We are a global player in the area of X-ray containment with lead (Pb). In addition to X-ray tube housings for medical imaging systems, we manufacture X-ray tube housings for the NDT and security industries, as well as components for nuclear medicine, together with solutions for nuclear waste management. Our CNC capabilities can be utilised for the development and industrialisation of medical equipment and instrument parts where the role of CNC is getting increasingly important thanks to its efficiency and cost. We are a global supplier shipping direct to production lines in Europe, the Middle East, Asia and North and South America. Our projects - from Prototype through to production supply are undertaken, all within the framework of a Quality Management System approved to ISO 9001: 2015 For more details, please consult our product and capabilities sections.





Health
Components for CT scanners and Vascular systems: X-Ray Tube Housings
X-ray tube housings provide radiation shielding, mechanical support and protection as well as a cooling oil hermetic containment for the imaging systems X-ray tube insert.
Delfield is supplying the major global medical imaging players with this critical component.
Delfield produces these housings both from castings and as ‘in-house’ fabricated aluminium dip-brazed assemblies.
Housings are lead-lined and painted 'in-house'.
Leak checking is performed 'in-house' by water immersion or vacuum, Helium mass spectrometer detection methods. We are a one-stop shop from prototype to production line implementation.
Calibration phantoms for Nuclear Medicine (Gamma cameras)
Phantoms are used to calibrate the imaging devices and to simulate your imaging.
Phantoms are manufactured in BAR, NEMA, LINEAR and FLOOD formats.
BAR Phantoms are utilized for the determination of the resolution of Gamma cameras. Four-quadrant phantom offers a precise determination of camera intrinsic resolution, collimator spatial resolution, field size and linearity.
Slot/hole patterns are in a lead top layer bonded to an aluminium or polycarbonate substrate.
The Phantoms can be supplied with a fabricated stand or as a kit with a shipping case.
Calibration certificates are available.
Collimators for Nuclear Medicine (Gamma cameras)
Another range of Nuclear Medicine components that utilise CNC machined lead is collimators.
A gamma camera collimator is designed to restrict the rays from the radioactive source reaching the camera detector so that each point in the image corresponds to a unique point in the patient's anatomy.
Collimators are composed of thousands of channels formed by folding and assembling lead foils. Only the gamma-ray photons emitted by the radioactive source that travel directly along the channel can reach the detector, while the other photons are absorbed by the collimator channel walls.
Nuclear Imaging: Gamma Ray Detector Casings and Radiotope Source Holders
Delfield manufactures Gamma camera detector casings.
The lead casings are given structural strength by having the lead cast around a steel insert. Additional strength may be gained by an externally mounted steel or aluminium 'jacket'.
Delfield also designs and manufactures the moulds and inserts for these castings. Point sources stored and handled in ad-hoc holders - are utilized to determine the limit of the camera/collimator spatial resolution.
They are based at variable distances closer and closer together along a ruler until the two imaged points can no longer be distinguished as distinct separate sources.

Defence
Waveguide components
The complex geometries of waveguide components demand high levels of precision in the manufacturing process. Delfield produces complex waveguide components leveraging its ‘in-house’ aluminium dip brazing, CNC machining and inspection capabilities.


Automotive
Impellers
Manufacturing impellers utilising the dip brazing technology comes with the advantages of low thermal stress and deformations avoidance. Dip brazing also gives more design freedom and cost competitiveness thanks to the complexity of the shapes and solutions it can support.
Heat exchangers
Delfield decade of experience in dip brazing in general and in particular in the manufacturing of leak-tight vessels gives it a particular edge when it comes to heat-exchangers production. Dip brazing plays a critical role to concurrently achieve the highest quality, cost efficiency and reliability.

Battery housings
Sealed battery boxes
Sealed battery boxes are efficiently produced thanks to aluminium dip brazing. From medical instruments to electric vehicles, batteries are increasingly pervasive and their housings require electrical insulation, resistance to shock, vibration and chemicals.
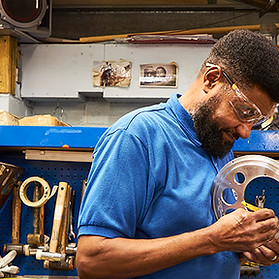
Water treatment
Valves and accessories for water treatment plants
Valves for water treatment plants oftentimes come equipped with actuators and other instruments. Delfield’s precision CNC coupled with dip brazing capabilities is instrumental in producing valves complying with the demands and conditions of water treatment plants.

Various industries
Machined components
Delfield offer an extensive CNC machining facility for the supply of precision components in both prototype and production batches.
Fabrications
Delfield manufactures components that require a combination of precision machining and metal fabrication techniques. Examples shown include sheet metal forming, spinning, laser cutting, brazing and welding.

Capabilities
CNC machining & assembling
Machined components
Delfield offer an extensive CNC machining facility for the supply of precision components in both prototype and production batches.
We manufacture a wide range of high-precision machined components with extremely tight tolerances for the following industries:
​
• Aerospace
• Defence
• Electronics
• Medical
• Water processing
Fabrications
Delfield manufacture components that require a combination of precision machining and metal fabrication techniques. Examples shown include sheet metal forming, spinning, laser cutting, brazing and welding.
​
Supporting processes
• Prototyping
• Product design
• Process selection
• Welding and fabrication
• Painting & plating
• Pressing
• Iridite
• Assembly
• Leak testing
• CMM inspection


Lead (Pb) lining
Lead metal is the preferred material for radiation shielding from nuclear reactors to medical X-ray labs. Lead can be used against various high-energy applications of radiation, including gamma rays, x-rays, and other types of nuclear radiation.
However since lead is a toxic material, it requires a controlled environment and equipment to safely handle the hazards of its manufacture and transport.
​
Delfield prides itself on being a leading manufacturer of lead products for the medical imaging industry. Delfield is experienced in the design, manufacture and fitting of lead linings to irregularly shaped bodies providing radiation shielding. We assist you from concept development and the engineering/design stage up to prototyping and then to production. Thanks to our comprehensive ‘in-house’ supporting processes including painting and inspection, we are our one-stop-shop for your advanced lead manufacturing needs.
​
​Supporting processes
-
R&D and design support
-
Torch brazing
-
Soldering
-
Welding
-
Painting
-
CMM inspection